Improved Tent Pole Reliability
Durston is pleased to have worked with Easton on a new manufacturing process that will improve the reliability of Easton tent poles.
Our first freestanding tent - the X-Dome 1+ - was released in late 2024. Soon after our customers let us know about a manufacturing issue with the tent poles where the aluminum inserts joining the sections were sometimes not glued well enough into place. As a result, the inserts would sometimes loosen and slide out of position - making the tent difficult to assemble and potentially leading to pole breakage.
Since then, we have learned this issue has also affected other tent brands using Easton poles. We take this very seriously because you need to be able to trust your gear in the backcountry. We quickly notified our customers and escalated this issue with Easton to improve their process. We also promised to proactively provide improved replacement poles to 100% of customers (rather than only replacing poles after a failure).
Through work with Easton, we were able to determine the root cause was improper glue application. More specifically, vulnerabilities in Easton's manufacturing process could result in little glue being applied and with insufficient dispersion.
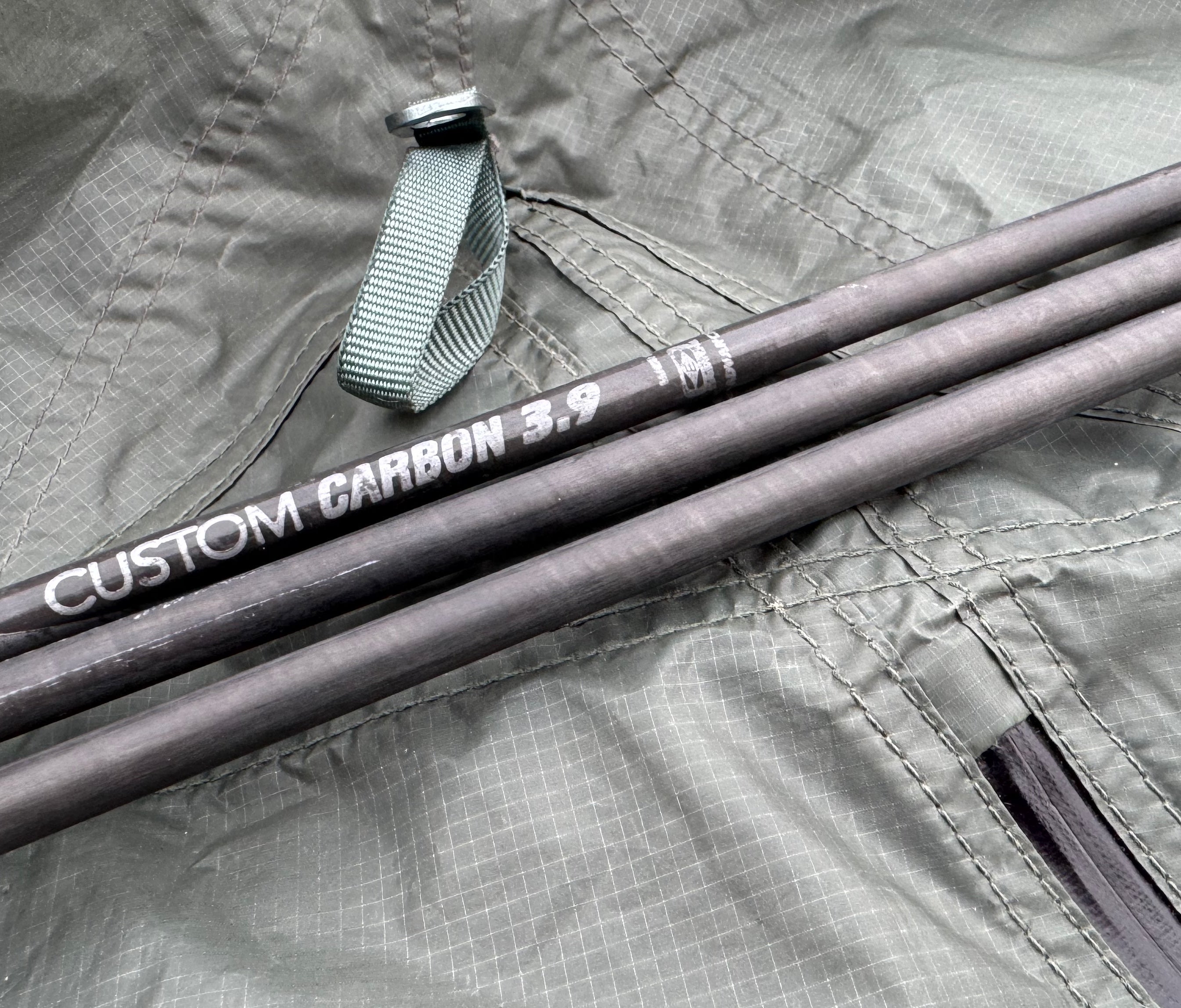
We appreciate Easton taking this issue seriously and devoting their engineering staff towards a robust fix. After a few months of hard work, we are pleased to announce a dramatically improved gluing process. With the old process the glue was dripped into the tube and this drip could potentially be pushed out of the way as the insert was added to leave 0-10% glue coverage. A subsequent spinning step intended to spread the glue was only partially effective. The new process dramatically improves the gluing results. This new process starts with an improved glue formulation and applies that in much greater amounts, while also spraying the glue with air pressure as it is applied over a wide area instead of as a drip. To ensure excellent coverage, an updated spinning process more reliably spins the shaft while holding the insert still, so all surfaces become reliably coated. Further QC process have also been added including laser etched batch IDs and higher testing standards during production that are more stringent and more frequent.

Testing of the new glue process has confirmed a dramatic improvement in the glue performance. That includes much higher results of over 1500 lbs (700 kg) in a pull test on the glued insert. A flex test also shows a drastic improvement. In this test the glued joint is weighted and flex cycled to simulate real world use of tent poles. Where the old glue process could sometimes fail in just a few cycles, the new glue process gives results over 100x better. The poles can flex for thousands of cycles with no observable degradation in the strength.
We apologize for the initial issue, and appreciate your patience as we have worked to find a solution. The initial issue was unfortunate but we are pleased to have worked with Easton to develop a solution that not only improves our tents but also has industry wide benefits, as this new production process is now being used for all Easton tent pole customers. We have now shipped out improved poles to 100% of first batch customers to restore their trust in the tent.
Dan Durston
President and Product Architect